Principle of ultrasonic welding:
The basic principle of ultrasonic plastic welding is to use the high-speed vibration of the welding die head exceeding 15KHZ per second, which is mechanically transmitted to the two plastic processing workpiece surfaces, generating local high temperature in an instant, causing the plastic interface to quickly melt. After the vibration stops, the melted parts are subjected to pressure to complete the fusion work before solidification.
Ultrasonic plastic welding machine is a universal and specialized equipment for welding plastic forming products, as well as for sealing plastic sheets, paper and aluminum composite films, and plastic hoses. Different processing methods such as fusion, embedding, and riveting are adopted according to the different objects.
Servo driven ultrasonic description:
The intelligent dynamic servo ultrasonic welding system integrates all electric servo technology to remove changes with pneumatic components, thereby improving the efficiency and accuracy of the process. The dynamic servo motion control technology improves the precision control of ultrasonic component speed, pressure, position, and a more powerful optimization process. Repeatable and precise servo motion control with higher efficiency and reliability. Improved production efficiency by 1.5-3 times compared to regular cylinder drive. Precise and constant speed and pressure control can be optimized for any combination in the initial application of ultrasonic energy. Programmable component speed, position, and torque (pressure) control. It is allowed to set the speed, position, and torque (pressure) during the welding phase, whether it is constant or segmented. Reduce cycle time. Simple calibration program without pneumatic components for adjustment. Suitable for integration into automatic assembly systems, with high accuracy and the need to reduce changes.
Advantages of servo driven ultrasonic systems:
1. By using distance control method, it is possible to more accurately control the distance between the weld seam and collapse. Closed loop servo position control is used to directly control distance and attempt to dynamically reach the desired position, thereby obtaining accurate and reproducible results. Make ultrasonic plastic products seamless, with a smooth and even surface.
2. Quickly change the speed. In specific applications, in order to match the melting rate of materials, a variable curve must be used to represent the welding speed during welding. The servo system can accelerate at a speed of 1.27 meters per second, which is equivalent to changing the speed to 0.0254 meters per second within 0.02 seconds.
Features:
1. No compressed air, integrated system control
2. 1.3-3 times higher production efficiency than regular cylinders
3. Multiple welding modes can be set in segments
4. Simultaneously providing pressure and depth welding modes
5. Process optimization that provides strong pressure and position
6. Precision speed and pressure control make welding more precise and stable
Application scope:
Servo driven ultrasonic welding machine, capable of handling difficult and high-precision welding tasks, especially suitable for products with high airtightness requirements such as medical, precision electronic components, and automotive parts.
Applicable products:
Automotive industry: plastic body parts, car doors, car instruments, car lights and mirrors, sunshades, interior parts, filters, reflective materials, reflective road studs, bumpers, cables, plastic filters for motorcycles, radiators, brake fluid tanks, oil cups, water tanks, fuel tanks, air ducts, exhaust purifiers, tray filters;
Plastic electronics: prepaid water and electricity meters, communication devices, cordless phones, mobile phone accessories, phone cases, battery cases, chargers, valve controlled sealed maintenance lead-acid batteries, 3-inch floppy disks, USB drives, SD cards, CF cards, USB connectors, Bluetooth;
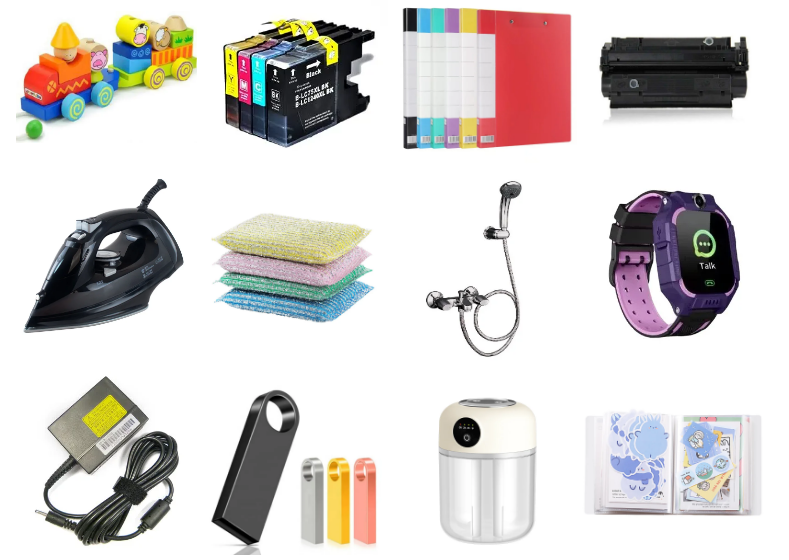
Toys and stationery:folders, photo albums, folding boxes, PP hollow boards, pen cases, ink cartridges, toner cartridges;
Medical daily use: watches, kitchenware, oral liquid bottle caps, drip bottle caps, mobile phone accessories, gold brushes, daily necessities;
Hygiene products: children's products, air mattresses, hangers, knife handles, gardening products, kitchen utensils, showerheads, shower heads, anti-counterfeiting bottle caps, cosmetics bottle caps, coffee pots, washing machines, air dehumidifiers, electric irons, electric kettles, vacuum cleaners, speaker metal covers, and civil grilles.
Different Material Matching Tables for Plastic Fusion Welding: